Share what you know,
and discover more.
Share what you know,
and discover more.
Jan 01, 2009
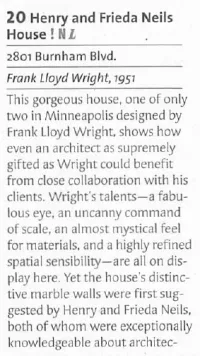
-
- Charmaine Bantugan
2801 Burnham Blvd, Minneapolis, MN, USA
2801 Burnham Blvd Home History Frank Lloyd Wright, 1951 This gorgeous house, one of only two in Minneapolis designed by Frank Lloyd Wright, shows how even an architect as supremely gifted as Wright could benefit from close collaboration with his clients. Wright's talents a fabulous eye, an uncanny command of scale, an almost mystical feel for materials, and a highly refined spatial sensibility-are all on dis- play here. Yet the house's distinctive marble walls were first suggested by Henry and Frieda Neils, both of whom were exceptionally knowledgeable about architecture and design. At the time the house was built, Henry was the retired president of the Flour City Ornamental Iron Co. in Minneapolis. Frieda was the artistically minded daughter of the iron company's founder and also an enthusiastic admirer of Wright's work. In 1949 the couple began making plans for a new home over- looking Cedar Lake on property adjoining their existing home, built in 1923, at 2815 Burnham Blvd. Believing Wright could give them just the house they wanted, the couple journeyed to the great architect's Wisconsin estate to meet with him. At some point they showed him a picture of their 1920s "Mediterranean" house. Wright agreed that they needed a new home and suggested-probably facetiously, though you never could tell with him-that they should "burn the old one down." The Neilses didn't follow that incendiary bit of advice, but they did indeed hire Wright to design their new home, with splendid results. In many ways the house is typical of the so-called Usonian designs that Wright developed in the 1930s. It's L shaped, has just one story (with no basement), uses a limited palette of materials, and is planned in a way that separates what Wright called "active" and "quiet" zones. The house's main "active" area is its living room, which features a 17-foot-high vaulted ceiling and offers views of the lake across a walled terrace. The long wing that extends into a triple carport holds the quiet area, devoted to bedrooms and a gallery connecting to the front door, which in typical Wrightian fashion is well hidden. The house is the only one Wright ever built with marble walls. The colored and textured walls, which taper as they rise, consist of small blocks of "cull" marble left over from other building projects. Henry Neils, who was a trustee of a marble and tile company, had acquired the stone at a good price and convinced Wright to use it. To achieve the effect he desired, Wright had the masons chip away any polished edges before laying up a piece of marble. How- ever, when the walls were finally completed, neither Wright nor his clients liked the overall color. Wright dispatched one of his students to supervise a process by which some blocks were stained to create just the right color effects. The home's aluminum windows, made by Neils's company, are also unique in Wright's residential work, since he generally preferred wooden frames. Neils's connection to a lumber company owned by his father resulted in another atypical feature: interior paneling made of western larch as opposed to the cypress or red- wood Wright usually preferred. In 2008 the house was sold to new owners after being in the Neils family for 57 years. ... Read More Read Less
2801 Burnham Blvd, Minneapolis, MN, USA
2801 Burnham Blvd Home History Frank Lloyd Wright, 1951 This gorgeous house, one of only two in Minneapolis designed by Frank Lloyd Wright, shows how even an architect as supremely gifted as Wright could benefit from close collaboration with his clients. Wright's talents a fabulous eye, an uncanny command of scale, an almost mystical feel for materials, and a highly refined spatial sensibility-are all on dis- play here. Yet the house's distinctive marble walls were first suggested by Henry and Frieda Neils, both of whom were exceptionally knowledgeable about architecture and design. At the time the house was built, Henry was the retired president of the Flour City Ornamental Iron Co. in Minneapolis. Frieda was the artistically minded daughter of the iron company's founder and also an enthusiastic admirer of Wright's work. In 1949 the couple began making plans for a new home over- looking Cedar Lake on property adjoining their existing home, built in 1923, at 2815 Burnham Blvd. Believing Wright could give them just the house they wanted, the couple journeyed to the great architect's Wisconsin estate to meet with him. At some point they showed him a picture of their 1920s "Mediterranean" house. Wright agreed that they needed a new home and suggested-probably facetiously, though you never could tell with him-that they should "burn the old one down." The Neilses didn't follow that incendiary bit of advice, but they did indeed hire Wright to design their new home, with splendid results. In many ways the house is typical of the so-called Usonian designs that Wright developed in the 1930s. It's L shaped, has just one story (with no basement), uses a limited palette of materials, and is planned in a way that separates what Wright called "active" and "quiet" zones. The house's main "active" area is its living room, which features a 17-foot-high vaulted ceiling and offers views of the lake across a walled terrace. The long wing that extends into a triple carport holds the quiet area, devoted to bedrooms and a gallery connecting to the front door, which in typical Wrightian fashion is well hidden. The house is the only one Wright ever built with marble walls. The colored and textured walls, which taper as they rise, consist of small blocks of "cull" marble left over from other building projects. Henry Neils, who was a trustee of a marble and tile company, had acquired the stone at a good price and convinced Wright to use it. To achieve the effect he desired, Wright had the masons chip away any polished edges before laying up a piece of marble. How- ever, when the walls were finally completed, neither Wright nor his clients liked the overall color. Wright dispatched one of his students to supervise a process by which some blocks were stained to create just the right color effects. The home's aluminum windows, made by Neils's company, are also unique in Wright's residential work, since he generally preferred wooden frames. Neils's connection to a lumber company owned by his father resulted in another atypical feature: interior paneling made of western larch as opposed to the cypress or red- wood Wright usually preferred. In 2008 the house was sold to new owners after being in the Neils family for 57 years. ... Read More Read Less
Jan 01, 2009
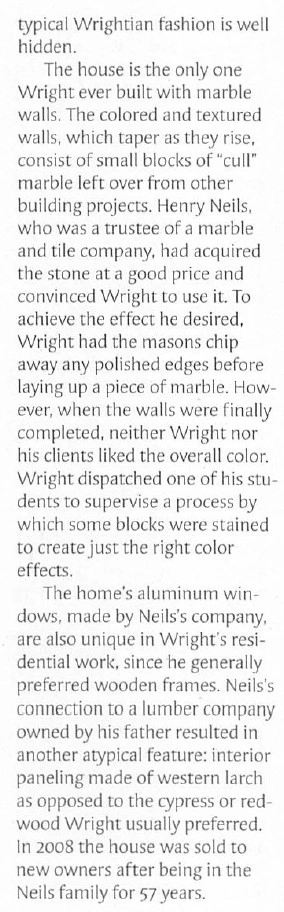
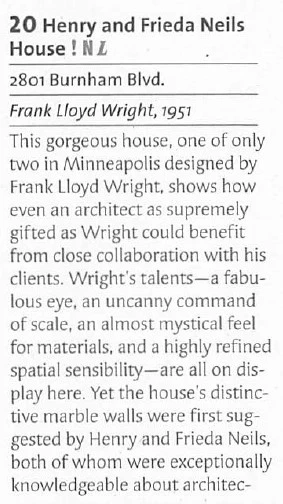
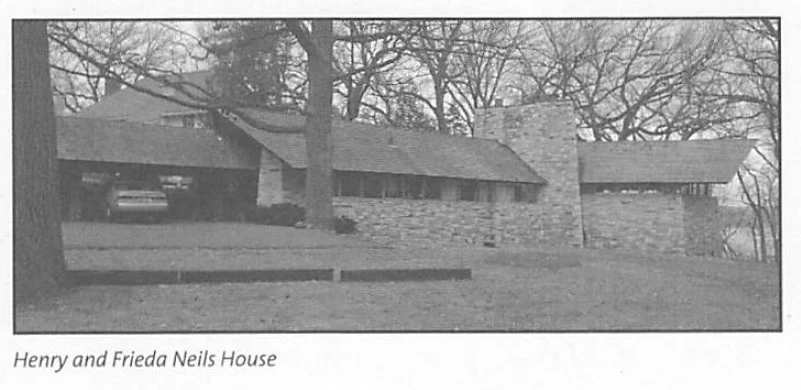
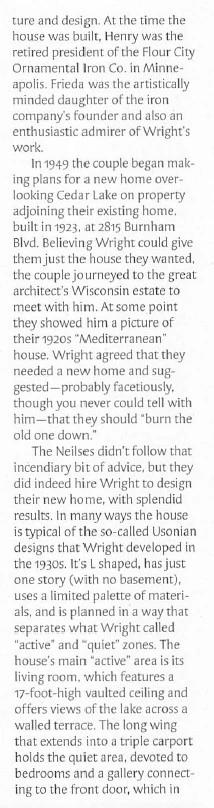
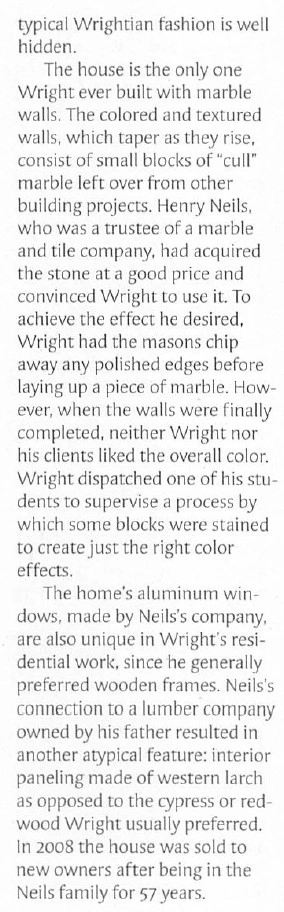
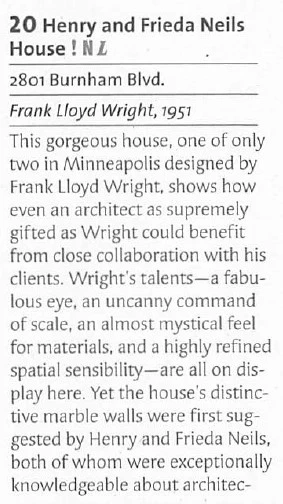
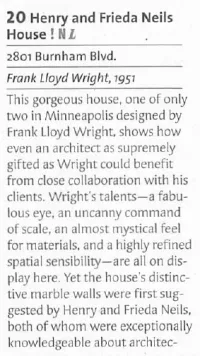
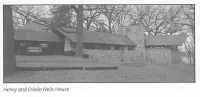
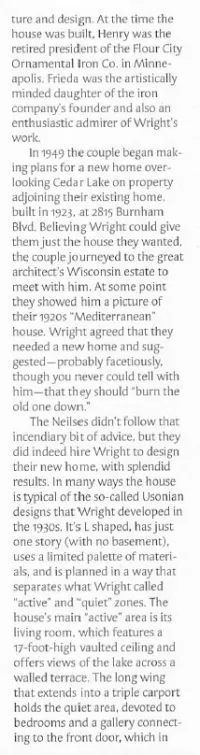
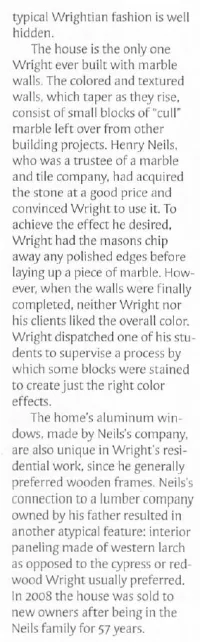
2801 Burnham Blvd, Minneapolis, MN, USA
2801 Burnham Blvd Home HistoryFrank Lloyd Wright, 1951
This gorgeous house, one of only two in Minneapolis designed by Frank Lloyd Wright, shows how even an architect as supremely gifted as Wright could benefit from close collaboration with his clients. Wright's talents a fabulous eye, an uncanny command of scale, an almost mystical feel for materials, and a highly refined spatial sensibility-are all on dis- play here. Yet the house's distinctive marble walls were first suggested by Henry and Frieda Neils, both of whom were exceptionally knowledgeable about architecture and design. At the time the house was built, Henry was the
retired president of the Flour City Ornamental Iron Co. in Minneapolis. Frieda was the artistically minded daughter of the iron company's founder and also an enthusiastic admirer of Wright's work.
In 1949 the couple began making plans for a new home over- looking Cedar Lake on property adjoining their existing home, built in 1923, at 2815 Burnham Blvd. Believing Wright could give them just the house they wanted, the couple journeyed to the great architect's Wisconsin estate to meet with him. At some point they showed him a picture of their 1920s "Mediterranean" house. Wright agreed that they needed a new home and suggested-probably facetiously, though you never could tell with him-that they should "burn the old one down."
The Neilses didn't follow that incendiary bit of advice, but they did indeed hire Wright to design their new home, with splendid results. In many ways the house is typical of the so-called Usonian designs that Wright developed in the 1930s. It's L shaped, has just one story (with no basement), uses a limited palette of materials, and is planned in a way that separates what Wright called "active" and "quiet" zones. The house's main "active" area is its living room, which features a 17-foot-high vaulted ceiling and offers views of the lake across a walled terrace. The long wing that extends into a triple carport holds the quiet area, devoted to bedrooms and a gallery connecting to the front door, which in typical Wrightian fashion is well hidden.
The house is the only one Wright ever built with marble walls. The colored and textured walls, which taper as they rise, consist of small blocks of "cull" marble left over from other building projects. Henry Neils, who was a trustee of a marble and tile company, had acquired the stone at a good price and convinced Wright to use it. To achieve the effect he desired, Wright had the masons chip away any polished edges before laying up a piece of marble. How- ever, when the walls were finally completed, neither Wright nor his clients liked the overall color. Wright dispatched one of his students to supervise a process by which some blocks were stained to create just the right color effects.
The home's aluminum windows, made by Neils's company, are also unique in Wright's residential work, since he generally preferred wooden frames. Neils's connection to a lumber company owned by his father resulted in another atypical feature: interior paneling made of western larch as opposed to the cypress or red- wood Wright usually preferred. In 2008 the house was sold to new owners after being in the Neils family for 57 years.
Posted Date
Sep 22, 2023
Historical Record Date
Jan 01, 2009
Source Name
AIA Guide to the Minneapolis Lake District
Delete Story
Are you sure you want to delete this story?
Feb 05, 2004
Feb 05, 2004
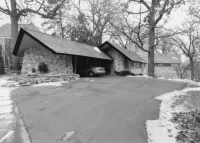
-
- Charmaine Bantugan
The Frieda and Henry J. Neils House - National Registry of Historic Places
Statement of Significance: The Frieda and Henry J. Neils House is eligible for the National Register under Criterion C as a property that embodies distinctive characteristics of a type, period or method of construction. It is of statewide significance in the area of architecture. The house is a good example of Frank Lloyd Wright’s post World War II Usonian houses. It is also a singular example because of its unique building materials - cull marble, clear Western larch and aluminum. It is the only house designed by Frank Lloyd Wright constructed of marble.’ Henry J. Neils, a prominent and well-connected Minneapolis businessman, not only suggested the unique building materials, but also was able to secure all of them through companies with which he was personally or professionally associated. The Frieda and Henry J. Neils House falls within the statewide historic context "Urban Centers, 1870-1940," and within the local contexts "Minneapolis Architecture: Post War Minneapolis, 1945-1991." The singularity of the house is a manifestation of the well-documented process of give and take between Henry J. Neils and Frank Lloyd Wright that characterized the design and construction phases. The process of designing and constructing the Neils house, and discussions about building material selection, are meticulously documented in extensive correspondence between Neils and Wright. Such correspondence proved necessary because Wright did not visit the Neils house site until after the house was built, and Neils’s visits to Taliesin were infrequent. Neils also kept careful records of contracts and expenditures. In 1949 Henry J. Neils, retired president of Flour City Ornamental Iron Company in Minneapolis, and his wife, Frieda Tetzlaff Neils, asked Frank Lloyd Wright to build a “one story modem functional house,” for them and their daughter Patricia, the youngest of their three children. They chose three lakeside lots that adjoined their 1923 thirteen-room family home at 2815 Burnham Boulevard in Minneapolis, as their building site. The Neils’s decision to approach Wright was an informed one. Collectively, Frieda and Henry were extremely knowledgeable about the arts, design, architecture, the building trade, and construction. Frieda Tetzlaff, Neils was the daughter of Eugene Tetzlaff who founded Flour City Ornamental Iron Company in Minneapolis in 1893. She frequently made extended visits to Europe with her parents where she became very interested in modem decorative arts and architecture. She was an avid collector of decorative arts, notably Meissen, Dresden, Venetian glass, and later Japanese and American ceramics. She was also a great admirer of the architecture and philosophies of Frank Lloyd Wright, and read widely on the subject. She suggested to her husband that Wright design their new home." Henry J. Neils was familiar with the building trade and accustomed to working with architects, contractors and craftsmen in his capacity as president of Flour City Ornamental Iron Company, a company that specialized in architectural metalwork and curtain wall windows, and which was also known for its artistry. Additionally, he was a scion of the J. Neils Lumber Company, founded by his father Julius, in Cass Lake, Minnesota, and a trustee of Northwestern Marble and Tile Corporation, Minneapolis. Although he once wrote to Wright saying, “Mrs. Neils and I are rank amateurs at this kind of work,” the correspondence suggests this was not the case. In an effort to connect with Wright, the Neilses sought the counsel of Dean and Mrs. Malcolm Willey, for whom Wright designed a house in 1934 in the Prospect Park neighborhood of Minneapolis.’ The Willey House was an important commission for Wright for several reasons. It was his first commission after years without work during the late 20s and early 30s, and ushered in a period of tremendous achievement and productivity for Wright; his very next commission was Fallingwater. But most significantly, the Willey House “represents the major bridge between the Prairie style and the soon-to appear standard L-plan Usonian house.” Mrs. (Nancy) Willey suggested they contact Eugene Masse link, Wright’s secretary, for an appointment with the architect. Prior to the arranged meeting, Neils sent Wright a letter in which he stated, “Mrs. Neils and I feel that only you could design a house that would take the best advantage of the beautiful view over Cedar Lake, On October 16,1949, the Neils’s and their elder daughter, Mary McGee, traveled to Taliesin in Spring Green, Wisconsin to meet with Wright. Upon showing Wright a photograph of their 1923 Mediterranean-style home, the architect immediately agreed that a new house was in order commenting, “You sure do need a new one; why don’t you bum the old one down? When asked by Wright what their requirements were for their new home, the Neils’s listed, “one level. a large living room, three small bedrooms each with a private bath, a kitchen and a carport.*’ They also specified a $25,000.00 maximum budget. On November 6, Wright sent a letter agreeing to take on the project. In a lengthy November 10th letter to Wright, Neils once again reiterated the family’s spatial requirements, and also described certain intangible qualities he sought in the design explaining, “As you know I am a lover of nature and enjoy the trees, water and beautiful sunsets over the lake. If the beautiful outdoors can be brought inside, this effect will give me a great deal of satisfaction.” He also added, “If you should decide on the use of aluminum, bronze, stainless steel, or just plain iron, our company is in a position to furnish such items. I am thinking particularly of window frames and mullions should the use of metal fit into your scheme of construction.” The Neilses were pleased with the plans they received from Wright in March of 1949. “You have interpreted our requirements perfectly,” Neils wrote. In the same letter Neils offered to “secure the necessary lumber from my brothers who operate a lumber mill at Libby, Montana and Klickitat, Washington,” listing Ponderosa pine, fir, larch, tamarack, some cedar and white pine as possible choices. He also reiterated his offer to fabricate aluminum windows and glazed doors at Flour City Ornamental Iron. “[Flour City owns] the dies for aluminum extrusions that will accommodate double strength, plate or thermopile glazing.” Wright’s design for the Neils house is rooted in his principles for “Usonia,” a democratic societal ideal for which the architect designed Usonian, or “affordable, beautiful housing for a democratic America,” specifically the American middle class. *^ In his 1943 autobiography, Wright stated that his Usonian houses were intended to, “liberate the people living in the house.” In order to do so he challenged his clients to “see life in somewhat simplified terms,” and believed it was “necessary to get rid of all unnecessary complications in construction.” The Usonian house was modularly planned on one level, and organized spatially into active and quiet areas, which Wright segregated using various, angled geometric floor plan configurations. Usonian houses featured dominant living rooms often with a window wall on one side, and a masonry “workspace,” or kitchen, and utility core. Wright eliminated basements as well as garages, which he replaced with more economical carports. Structurally, the Usonian house stood on a concrete slab within which gravity heating was integrated. Wright felt it was ideal to “complete the building in one operation as it goes along the house is finished on the inside as it is completed outside.” To this end he employed sandwich wall construction, and favored five construction materials: wood, brick, cement, paper and glass. The Herbert and Katherine Jacobs Residence (Jacobs 1) built in 1936 in Madison, Wisconsin, was the first of Wright’s built houses that he described as “Usonian” The L-shaped plan of the house accommodates quiet areas in one wing and active in the other, and includes a large dominant living room, and masonry workplace core at the intersection of the two wings. The house, which cost $5,500. to build, was constructed of relatively inexpensive materials including brick, redwood and pine boards, and employed several efficient, low-cost building techniques, such as sandwich wall construction, and simplified, efficient design elements, such as gravity heating and a flat roof In that regard it is typical of the simply planned, inexpensively constructed Depression-era Usonians. Over time, however, Wright designed scores of Usonian houses that varied in composition and complexity with regard to geometry, size, materials, and structural elements. Wright also experimented with numerous roof configurations and cantilevers. While Depression-era Usonian houses featured inexpensive materials reflective of lean economic times, “masonry construction became the standard after WWI.” In plan, the Neils House bears many of the hallmarks of Wright’s Usonian houses and in this regard is closely related to Wright’s first Usonian, the Jacobs I House. These hallmarks include modular planning, one-level construction, social and spatial organization of the house into active and quiet areas, dominant size and placement of the living room, a masonry workspace core, and concrete slab floor with integrated gravity heating. The plan was originally generated on a 4’0” modular grid but was later reduced to a 3’6” grid to reduce costs. The impact of the module reduction is evident in narrow “gallery,” or hallway passage and several compact rooms. The layout of the house is one of many variations of the in-line plan Wright used for his Usonian houses. Other characteristic features include integrated lighting and furniture, and a non-load bearing window wall. Generally speaking, the more expensive building materials and masonry construction of the Neils house are typical of Wright’s post-World War II Usonians, which reflect postwar economic recovery, more generous home-owner budgets, and the commercial availability of an increasingly wide range of building materials. However, the Neils house is completely unique among Wright’s houses in the specific building materials used. The house is constructed of cull or scrap marble, clear Western larch interior tongue and groove walls, and custom-made aluminum windows and doors -- materials Wright never specified for his Usonian homes. All the materials were expensive on the retail market, and were either: unusual or not readily available (cull marble); not generally used for the purpose employed in the Neils house (clear Western larch for interior walls); or were used in commercial, not residential, construction (die-extruded aluminum windows and doors.) Uniquely, all three of these unusual and expensive materials were readily - and affordably - available to Henry Neils through three companies with which he was personally or professionally associated. They are respectively: Northwestern Marble and Tile Corporation, of which Neils was a trustee; the J. Neils Lumber Company, founded by Neils’s father Julius, and operated by two of his brothers, and; Flour City Ornamental Iron Company, founded by his father-in-law, Eugene Tetzlaff, and of which Neils was president. Through this fortunate set of circumstances, these more expensive and unusual construction materials proved to be the most economical and accessible choices for the house. Although it cannot be discerned precisely from the correspondence which materials Wright originally specified for the house, Mary McGee recalls fieldstone, brick, concrete block, and Tidewater cypress being mentioned in conversations. However, it can be discerned that Henry Neils repeatedly suggested materials and products, and forwarded pertinent product literature and material samples to Wright on a regular basis. Wright and Neils’s choice of materials, and the availability of these materials for residential construction, link the Neils house to post World War II economic prosperity, and identify it as a postwar Usonian. The most distinctive features of the house are the cull marble bearing walls and the process through which they were realized. Wright was receptive, but needed to be convinced, that cull marble could and should be used for the double or sandwich wall construction of the house. Frieda and Henry Neils set out to convince him. They went to Northwestern Marble and Tile Corporation and examined “piles of marble culls,” left over from myriad major construction projects, such as federal buildings (including the Minneapolis Post Office), courthouses, banks (including the Northwestern Bank building in Minneapolis) and hotels, undertaken by the firm. They selected nine samples of marble to send to Wright for consideration. The samples included Roman Travertine, Gray Tennessee, Montana Travertine, Colorado Travertine, Rose Bonnard, Batticon, Radio Black, Carthage and Verde Antique in pieces measuring fi-om 2” - 12” wide and from 6” to 30” long. In a succinct note Wright responded: “Regarding the marble. Take over all larger chunks and larger pieces (see drawing forwarded) and mix. Make a model wall and send photographs.” Wright approved the sample wall shortly thereafter. Wright eventually designed a double wall system lined with 2-inch rigid cork insulation. As constructed, the walls can’t, or taper from the ground up being approximately 30 inches thick at the bottom of the wall and 7 inches at the top. Wright also directed the stonemasons to roughly chip away the polished edges of the cull marble pieces to minimize the smooth and shiny appearance of polished block surfaces and edges. Stonemasons accomplished this labor-intensive step on site, one block at a time, by hand. Furthermore, Wright required the mortar be raked horizontally only to minimize any verticals. Although the walls were built to Wright’s specification, when the house was finished both architect and client expressed displeasure at the light color and visual dominance of some of the marble blocks. On Wright’s instruction, Taliesin apprentice John DeKoven Hill was dispatched supervise the hand staining of selected offending blocks. Although the applied coloration has faded on the exterior blocks, traces remain on some interior blocks. The clear Western larch was another unusual choice of wood for the house. Larch, a pinewood, was not commonly used for interior residential paneling. Rather it was more often used commercially, or for flooring and decking because of its durability. Additionally, the larch chosen was relatively rare being clear, or free of knotholes. This made the choice both particularly distinctive and potentially more expensive — were it not for Neils’s family lumber business connections. Although Neils initially priced out Tidewater red cypress, a wood Wright favored and suggested for the paneling, on more than one occasion he told Wright he could secure larch at less than half the cost of cypress through his brothers at J. Neils Lumber Company. Neils respectfully wrote Wright: “the choice of wood Mrs. Neils and I will leave entirely to you. We know you are interested in getting a certain result and if the larch will not produce it, of course, we will not use it. But diplomatically continued, “If, however, larch is satisfactory we can make quite a substantial saving in the cost of the house.” A week later Wright approved the use of larch. Neils was also responsible for the choice of aluminum for the windows and doors, prevailing over Wright’s preference for redwood. Once again, Neils was able to suggest a superior and affordable product that he, as president Flour City Ornamental Iron Company, could deliver. As early as March 1949, Neils made the connection between the number of windows and doors and their variety of shapes and sizes, and the wisdom of designing and fabricating them in aluminum. Although Flour City was producing window walls for large commercial projects across the nation, they were not in the residential window business. However, Neils told Wright that Flour City had “the necessary dies for aluminum extrusions that will accommodate double strength, plate of thermopile glazing.”^* He further stated that the installation of aluminum doors and windows in the Neils house would “undoubtedly be a tribute to our company.” Flour City also provided stainless steel counter tops in the kitchen (at Mrs. Neils’s request) replacing the linoleum countertops specified by Wright. Much of the spatial dynamism of Wright’s design for the Neils house is derived from visual illogic of the load of the roof being supported by an unbroken expanse of light aluminum window that rise to meet the roof and wrap the north and east living room walls. The design presented technical challenges that were further complicated when Wright revised his original plans by removing a marble structural pier from the northeast comer of the living room. Wright pushed the structural drama to its limit when he specified that the mullions must “present thin edges to view and be as light in appearance as possible. It fell to Flour City window designer George B. Melcher and general contractor Lyle Halverson, vice-president and general manager of Madsen Construction Company, to find an acceptable solution.^® In the end, “stainless steel bars of sufficient size and strength,” used as mullions for the windows provided adequate structural support while maintaining a light appearance. Originally, Wright designed a hipped roof or the Neils house, but later changed it to a gable roof with as5mimetrical planes. It is likely that Wright’s disdain of the house next door (the Neilses’s 1923 house) drove the redesign of the roof, as well as the orientation of the house on its site. Wright effectively blocked any view of the offending house by extending a section of the west plane of the gable roof to within inches of the ground. In a dramatic counterpoint, on the east side of the living room, the gable peaks seventeen feet above the ground and projects several feet beyond the window wall. The unequally sloped roof set up several unique conditions in the Neils house including the elimination of door-height soffits. According to Curtis Be singer, the Taliesin apprentice who prepared the working drawings for the Neils House, Wright often employed door-height soffits in his designs to establish “the intimate scale, horizontal layering of the space, its spatial contrasts, and the spatial continuity between the exterior and interior. In the absence of this ordering principle, the interior spaces have “increased plasticity,” and “a new sense of openness and freedom.” The absence of soffits also eliminated any space between them and the roof joists within which structural members could be concealed. As such, “any structural reinforcement of the roof-with steel beams or channels - now had to be handled within the roof thickness,” which is the case in the Neils house. Although Neils told Wright in December of 1949 that he and Mrs. Neils “would like to avail ourselves of Section 3 of our contract with you under which you will send an apprentice to select the proper contractor and supervise the work until the structure is satisfactorily completed,” this did not happen. Eugene Masselink explained to Neils: “Mr. Wright does not know what advantage an apprentice would be to you at this time.” Instead, Neils interviewed contractors and hired Lyle Halverson and Madsen Construction Company as general contractors. Neils and Halverson supervised and troubleshot the construction of the house while constantly communicating with Wright by mail. The relationship between Taliesin, and Neils and the construction team in Minneapolis was close and productive. According to Mary McGee, “their ability to communicate was a major factor in the successful building operation.” At Taliesin, chief draftsman John Howe instructed apprentice John Geiger to undertake the Neils house working drawings, which Steve Oyakawa later completed. After Wright made revisions, apprentice Curtis Be singer redrew the working drawings. Apprentice John DeKoven Hill worked most closely with the Neilses and was the only apprentice to visit the house while under construction. At Wright’s request, he supervised the staining of the marble blocks. But he also worked closely with the Neilses in his capacity as editorial director for House Beautiful magazine assisting with furniture and fabric selection. Hill was no doubt responsible for publishing photographs of the house in House Beautiful in November of 1955. The house was also photographed by several noted architectural photographers including Ezra Stoller, for Architectural Forum, and Pedro Guerrero, whose photographs appeared in House + Home. Wright visited the house on three occasions. The first time was three and a half years after completion of the house, in October 1954, when he came to lecture at the University of Minnesota and was a houseguest of the Neilses. The Neils house has had only two sets of owners - all members of the Neils family. Frieda Neils lived in the house until her death in 1975. Henry stayed on until 1977 when he remarried. In 1977 Mary McGee, elder daughter of Frieda and Henry Neils, and her husband J. Paul McGee purchased the house. Mary McGee currently resides in the Neils house. The Neils house generated a second commission for Wright from the Neils family. In 1954, Wright designed a house for Patricia Neils Boulter and her husband Cedric Boulter in Cincinnati, Ohio. The Neils house represents an excellent example of Frank Lloyd Wright’s postwar Usonian designs that evolved from his first Usonian, the Jacobs I house built in 1936, to the mature versions of the 1950s. Initially, straightforward plans and inexpensive materials characterized Usonian houses. After the Great Depression and the end of World War II, the designs increased in complexity and more expensive materials were often employed. The Neils house, through its complex massing, dramatic cantilevers, and the unique use of marble masonry. Western larch and aluminum doors and windows, represents a well-developed, important, and unique Usonian design by Frank Lloyd Wright from the postwar period. ... Read More Read Less
The Frieda and Henry J. Neils House - National Registry of Historic Places
Statement of Significance: The Frieda and Henry J. Neils House is eligible for the National Register under Criterion C as a property that embodies distinctive characteristics of a type, period or method of construction. It is of statewide significance in the area of architecture. The house is a good example of Frank Lloyd Wright’s post World War II Usonian houses. It is also a singular example because of its unique building materials - cull marble, clear Western larch and aluminum. It is the only house designed by Frank Lloyd Wright constructed of marble.’ Henry J. Neils, a prominent and well-connected Minneapolis businessman, not only suggested the unique building materials, but also was able to secure all of them through companies with which he was personally or professionally associated. The Frieda and Henry J. Neils House falls within the statewide historic context "Urban Centers, 1870-1940," and within the local contexts "Minneapolis Architecture: Post War Minneapolis, 1945-1991." The singularity of the house is a manifestation of the well-documented process of give and take between Henry J. Neils and Frank Lloyd Wright that characterized the design and construction phases. The process of designing and constructing the Neils house, and discussions about building material selection, are meticulously documented in extensive correspondence between Neils and Wright. Such correspondence proved necessary because Wright did not visit the Neils house site until after the house was built, and Neils’s visits to Taliesin were infrequent. Neils also kept careful records of contracts and expenditures. In 1949 Henry J. Neils, retired president of Flour City Ornamental Iron Company in Minneapolis, and his wife, Frieda Tetzlaff Neils, asked Frank Lloyd Wright to build a “one story modem functional house,” for them and their daughter Patricia, the youngest of their three children. They chose three lakeside lots that adjoined their 1923 thirteen-room family home at 2815 Burnham Boulevard in Minneapolis, as their building site. The Neils’s decision to approach Wright was an informed one. Collectively, Frieda and Henry were extremely knowledgeable about the arts, design, architecture, the building trade, and construction. Frieda Tetzlaff, Neils was the daughter of Eugene Tetzlaff who founded Flour City Ornamental Iron Company in Minneapolis in 1893. She frequently made extended visits to Europe with her parents where she became very interested in modem decorative arts and architecture. She was an avid collector of decorative arts, notably Meissen, Dresden, Venetian glass, and later Japanese and American ceramics. She was also a great admirer of the architecture and philosophies of Frank Lloyd Wright, and read widely on the subject. She suggested to her husband that Wright design their new home." Henry J. Neils was familiar with the building trade and accustomed to working with architects, contractors and craftsmen in his capacity as president of Flour City Ornamental Iron Company, a company that specialized in architectural metalwork and curtain wall windows, and which was also known for its artistry. Additionally, he was a scion of the J. Neils Lumber Company, founded by his father Julius, in Cass Lake, Minnesota, and a trustee of Northwestern Marble and Tile Corporation, Minneapolis. Although he once wrote to Wright saying, “Mrs. Neils and I are rank amateurs at this kind of work,” the correspondence suggests this was not the case. In an effort to connect with Wright, the Neilses sought the counsel of Dean and Mrs. Malcolm Willey, for whom Wright designed a house in 1934 in the Prospect Park neighborhood of Minneapolis.’ The Willey House was an important commission for Wright for several reasons. It was his first commission after years without work during the late 20s and early 30s, and ushered in a period of tremendous achievement and productivity for Wright; his very next commission was Fallingwater. But most significantly, the Willey House “represents the major bridge between the Prairie style and the soon-to appear standard L-plan Usonian house.” Mrs. (Nancy) Willey suggested they contact Eugene Masse link, Wright’s secretary, for an appointment with the architect. Prior to the arranged meeting, Neils sent Wright a letter in which he stated, “Mrs. Neils and I feel that only you could design a house that would take the best advantage of the beautiful view over Cedar Lake, On October 16,1949, the Neils’s and their elder daughter, Mary McGee, traveled to Taliesin in Spring Green, Wisconsin to meet with Wright. Upon showing Wright a photograph of their 1923 Mediterranean-style home, the architect immediately agreed that a new house was in order commenting, “You sure do need a new one; why don’t you bum the old one down? When asked by Wright what their requirements were for their new home, the Neils’s listed, “one level. a large living room, three small bedrooms each with a private bath, a kitchen and a carport.*’ They also specified a $25,000.00 maximum budget. On November 6, Wright sent a letter agreeing to take on the project. In a lengthy November 10th letter to Wright, Neils once again reiterated the family’s spatial requirements, and also described certain intangible qualities he sought in the design explaining, “As you know I am a lover of nature and enjoy the trees, water and beautiful sunsets over the lake. If the beautiful outdoors can be brought inside, this effect will give me a great deal of satisfaction.” He also added, “If you should decide on the use of aluminum, bronze, stainless steel, or just plain iron, our company is in a position to furnish such items. I am thinking particularly of window frames and mullions should the use of metal fit into your scheme of construction.” The Neilses were pleased with the plans they received from Wright in March of 1949. “You have interpreted our requirements perfectly,” Neils wrote. In the same letter Neils offered to “secure the necessary lumber from my brothers who operate a lumber mill at Libby, Montana and Klickitat, Washington,” listing Ponderosa pine, fir, larch, tamarack, some cedar and white pine as possible choices. He also reiterated his offer to fabricate aluminum windows and glazed doors at Flour City Ornamental Iron. “[Flour City owns] the dies for aluminum extrusions that will accommodate double strength, plate or thermopile glazing.” Wright’s design for the Neils house is rooted in his principles for “Usonia,” a democratic societal ideal for which the architect designed Usonian, or “affordable, beautiful housing for a democratic America,” specifically the American middle class. *^ In his 1943 autobiography, Wright stated that his Usonian houses were intended to, “liberate the people living in the house.” In order to do so he challenged his clients to “see life in somewhat simplified terms,” and believed it was “necessary to get rid of all unnecessary complications in construction.” The Usonian house was modularly planned on one level, and organized spatially into active and quiet areas, which Wright segregated using various, angled geometric floor plan configurations. Usonian houses featured dominant living rooms often with a window wall on one side, and a masonry “workspace,” or kitchen, and utility core. Wright eliminated basements as well as garages, which he replaced with more economical carports. Structurally, the Usonian house stood on a concrete slab within which gravity heating was integrated. Wright felt it was ideal to “complete the building in one operation as it goes along the house is finished on the inside as it is completed outside.” To this end he employed sandwich wall construction, and favored five construction materials: wood, brick, cement, paper and glass. The Herbert and Katherine Jacobs Residence (Jacobs 1) built in 1936 in Madison, Wisconsin, was the first of Wright’s built houses that he described as “Usonian” The L-shaped plan of the house accommodates quiet areas in one wing and active in the other, and includes a large dominant living room, and masonry workplace core at the intersection of the two wings. The house, which cost $5,500. to build, was constructed of relatively inexpensive materials including brick, redwood and pine boards, and employed several efficient, low-cost building techniques, such as sandwich wall construction, and simplified, efficient design elements, such as gravity heating and a flat roof In that regard it is typical of the simply planned, inexpensively constructed Depression-era Usonians. Over time, however, Wright designed scores of Usonian houses that varied in composition and complexity with regard to geometry, size, materials, and structural elements. Wright also experimented with numerous roof configurations and cantilevers. While Depression-era Usonian houses featured inexpensive materials reflective of lean economic times, “masonry construction became the standard after WWI.” In plan, the Neils House bears many of the hallmarks of Wright’s Usonian houses and in this regard is closely related to Wright’s first Usonian, the Jacobs I House. These hallmarks include modular planning, one-level construction, social and spatial organization of the house into active and quiet areas, dominant size and placement of the living room, a masonry workspace core, and concrete slab floor with integrated gravity heating. The plan was originally generated on a 4’0” modular grid but was later reduced to a 3’6” grid to reduce costs. The impact of the module reduction is evident in narrow “gallery,” or hallway passage and several compact rooms. The layout of the house is one of many variations of the in-line plan Wright used for his Usonian houses. Other characteristic features include integrated lighting and furniture, and a non-load bearing window wall. Generally speaking, the more expensive building materials and masonry construction of the Neils house are typical of Wright’s post-World War II Usonians, which reflect postwar economic recovery, more generous home-owner budgets, and the commercial availability of an increasingly wide range of building materials. However, the Neils house is completely unique among Wright’s houses in the specific building materials used. The house is constructed of cull or scrap marble, clear Western larch interior tongue and groove walls, and custom-made aluminum windows and doors -- materials Wright never specified for his Usonian homes. All the materials were expensive on the retail market, and were either: unusual or not readily available (cull marble); not generally used for the purpose employed in the Neils house (clear Western larch for interior walls); or were used in commercial, not residential, construction (die-extruded aluminum windows and doors.) Uniquely, all three of these unusual and expensive materials were readily - and affordably - available to Henry Neils through three companies with which he was personally or professionally associated. They are respectively: Northwestern Marble and Tile Corporation, of which Neils was a trustee; the J. Neils Lumber Company, founded by Neils’s father Julius, and operated by two of his brothers, and; Flour City Ornamental Iron Company, founded by his father-in-law, Eugene Tetzlaff, and of which Neils was president. Through this fortunate set of circumstances, these more expensive and unusual construction materials proved to be the most economical and accessible choices for the house. Although it cannot be discerned precisely from the correspondence which materials Wright originally specified for the house, Mary McGee recalls fieldstone, brick, concrete block, and Tidewater cypress being mentioned in conversations. However, it can be discerned that Henry Neils repeatedly suggested materials and products, and forwarded pertinent product literature and material samples to Wright on a regular basis. Wright and Neils’s choice of materials, and the availability of these materials for residential construction, link the Neils house to post World War II economic prosperity, and identify it as a postwar Usonian. The most distinctive features of the house are the cull marble bearing walls and the process through which they were realized. Wright was receptive, but needed to be convinced, that cull marble could and should be used for the double or sandwich wall construction of the house. Frieda and Henry Neils set out to convince him. They went to Northwestern Marble and Tile Corporation and examined “piles of marble culls,” left over from myriad major construction projects, such as federal buildings (including the Minneapolis Post Office), courthouses, banks (including the Northwestern Bank building in Minneapolis) and hotels, undertaken by the firm. They selected nine samples of marble to send to Wright for consideration. The samples included Roman Travertine, Gray Tennessee, Montana Travertine, Colorado Travertine, Rose Bonnard, Batticon, Radio Black, Carthage and Verde Antique in pieces measuring fi-om 2” - 12” wide and from 6” to 30” long. In a succinct note Wright responded: “Regarding the marble. Take over all larger chunks and larger pieces (see drawing forwarded) and mix. Make a model wall and send photographs.” Wright approved the sample wall shortly thereafter. Wright eventually designed a double wall system lined with 2-inch rigid cork insulation. As constructed, the walls can’t, or taper from the ground up being approximately 30 inches thick at the bottom of the wall and 7 inches at the top. Wright also directed the stonemasons to roughly chip away the polished edges of the cull marble pieces to minimize the smooth and shiny appearance of polished block surfaces and edges. Stonemasons accomplished this labor-intensive step on site, one block at a time, by hand. Furthermore, Wright required the mortar be raked horizontally only to minimize any verticals. Although the walls were built to Wright’s specification, when the house was finished both architect and client expressed displeasure at the light color and visual dominance of some of the marble blocks. On Wright’s instruction, Taliesin apprentice John DeKoven Hill was dispatched supervise the hand staining of selected offending blocks. Although the applied coloration has faded on the exterior blocks, traces remain on some interior blocks. The clear Western larch was another unusual choice of wood for the house. Larch, a pinewood, was not commonly used for interior residential paneling. Rather it was more often used commercially, or for flooring and decking because of its durability. Additionally, the larch chosen was relatively rare being clear, or free of knotholes. This made the choice both particularly distinctive and potentially more expensive — were it not for Neils’s family lumber business connections. Although Neils initially priced out Tidewater red cypress, a wood Wright favored and suggested for the paneling, on more than one occasion he told Wright he could secure larch at less than half the cost of cypress through his brothers at J. Neils Lumber Company. Neils respectfully wrote Wright: “the choice of wood Mrs. Neils and I will leave entirely to you. We know you are interested in getting a certain result and if the larch will not produce it, of course, we will not use it. But diplomatically continued, “If, however, larch is satisfactory we can make quite a substantial saving in the cost of the house.” A week later Wright approved the use of larch. Neils was also responsible for the choice of aluminum for the windows and doors, prevailing over Wright’s preference for redwood. Once again, Neils was able to suggest a superior and affordable product that he, as president Flour City Ornamental Iron Company, could deliver. As early as March 1949, Neils made the connection between the number of windows and doors and their variety of shapes and sizes, and the wisdom of designing and fabricating them in aluminum. Although Flour City was producing window walls for large commercial projects across the nation, they were not in the residential window business. However, Neils told Wright that Flour City had “the necessary dies for aluminum extrusions that will accommodate double strength, plate of thermopile glazing.”^* He further stated that the installation of aluminum doors and windows in the Neils house would “undoubtedly be a tribute to our company.” Flour City also provided stainless steel counter tops in the kitchen (at Mrs. Neils’s request) replacing the linoleum countertops specified by Wright. Much of the spatial dynamism of Wright’s design for the Neils house is derived from visual illogic of the load of the roof being supported by an unbroken expanse of light aluminum window that rise to meet the roof and wrap the north and east living room walls. The design presented technical challenges that were further complicated when Wright revised his original plans by removing a marble structural pier from the northeast comer of the living room. Wright pushed the structural drama to its limit when he specified that the mullions must “present thin edges to view and be as light in appearance as possible. It fell to Flour City window designer George B. Melcher and general contractor Lyle Halverson, vice-president and general manager of Madsen Construction Company, to find an acceptable solution.^® In the end, “stainless steel bars of sufficient size and strength,” used as mullions for the windows provided adequate structural support while maintaining a light appearance. Originally, Wright designed a hipped roof or the Neils house, but later changed it to a gable roof with as5mimetrical planes. It is likely that Wright’s disdain of the house next door (the Neilses’s 1923 house) drove the redesign of the roof, as well as the orientation of the house on its site. Wright effectively blocked any view of the offending house by extending a section of the west plane of the gable roof to within inches of the ground. In a dramatic counterpoint, on the east side of the living room, the gable peaks seventeen feet above the ground and projects several feet beyond the window wall. The unequally sloped roof set up several unique conditions in the Neils house including the elimination of door-height soffits. According to Curtis Be singer, the Taliesin apprentice who prepared the working drawings for the Neils House, Wright often employed door-height soffits in his designs to establish “the intimate scale, horizontal layering of the space, its spatial contrasts, and the spatial continuity between the exterior and interior. In the absence of this ordering principle, the interior spaces have “increased plasticity,” and “a new sense of openness and freedom.” The absence of soffits also eliminated any space between them and the roof joists within which structural members could be concealed. As such, “any structural reinforcement of the roof-with steel beams or channels - now had to be handled within the roof thickness,” which is the case in the Neils house. Although Neils told Wright in December of 1949 that he and Mrs. Neils “would like to avail ourselves of Section 3 of our contract with you under which you will send an apprentice to select the proper contractor and supervise the work until the structure is satisfactorily completed,” this did not happen. Eugene Masselink explained to Neils: “Mr. Wright does not know what advantage an apprentice would be to you at this time.” Instead, Neils interviewed contractors and hired Lyle Halverson and Madsen Construction Company as general contractors. Neils and Halverson supervised and troubleshot the construction of the house while constantly communicating with Wright by mail. The relationship between Taliesin, and Neils and the construction team in Minneapolis was close and productive. According to Mary McGee, “their ability to communicate was a major factor in the successful building operation.” At Taliesin, chief draftsman John Howe instructed apprentice John Geiger to undertake the Neils house working drawings, which Steve Oyakawa later completed. After Wright made revisions, apprentice Curtis Be singer redrew the working drawings. Apprentice John DeKoven Hill worked most closely with the Neilses and was the only apprentice to visit the house while under construction. At Wright’s request, he supervised the staining of the marble blocks. But he also worked closely with the Neilses in his capacity as editorial director for House Beautiful magazine assisting with furniture and fabric selection. Hill was no doubt responsible for publishing photographs of the house in House Beautiful in November of 1955. The house was also photographed by several noted architectural photographers including Ezra Stoller, for Architectural Forum, and Pedro Guerrero, whose photographs appeared in House + Home. Wright visited the house on three occasions. The first time was three and a half years after completion of the house, in October 1954, when he came to lecture at the University of Minnesota and was a houseguest of the Neilses. The Neils house has had only two sets of owners - all members of the Neils family. Frieda Neils lived in the house until her death in 1975. Henry stayed on until 1977 when he remarried. In 1977 Mary McGee, elder daughter of Frieda and Henry Neils, and her husband J. Paul McGee purchased the house. Mary McGee currently resides in the Neils house. The Neils house generated a second commission for Wright from the Neils family. In 1954, Wright designed a house for Patricia Neils Boulter and her husband Cedric Boulter in Cincinnati, Ohio. The Neils house represents an excellent example of Frank Lloyd Wright’s postwar Usonian designs that evolved from his first Usonian, the Jacobs I house built in 1936, to the mature versions of the 1950s. Initially, straightforward plans and inexpensive materials characterized Usonian houses. After the Great Depression and the end of World War II, the designs increased in complexity and more expensive materials were often employed. The Neils house, through its complex massing, dramatic cantilevers, and the unique use of marble masonry. Western larch and aluminum doors and windows, represents a well-developed, important, and unique Usonian design by Frank Lloyd Wright from the postwar period. ... Read More Read Less
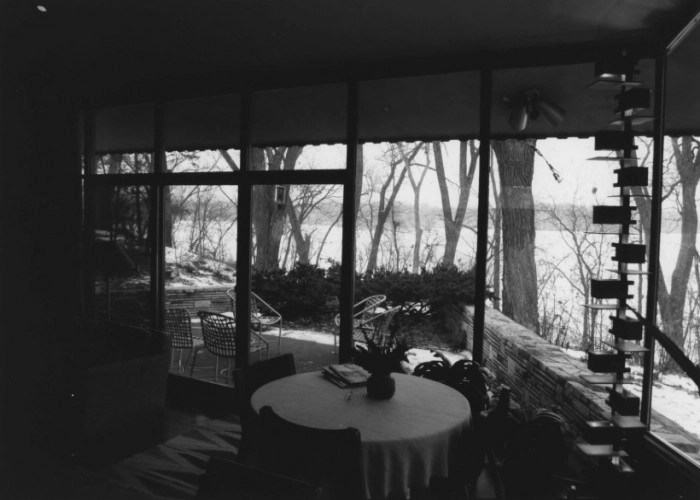
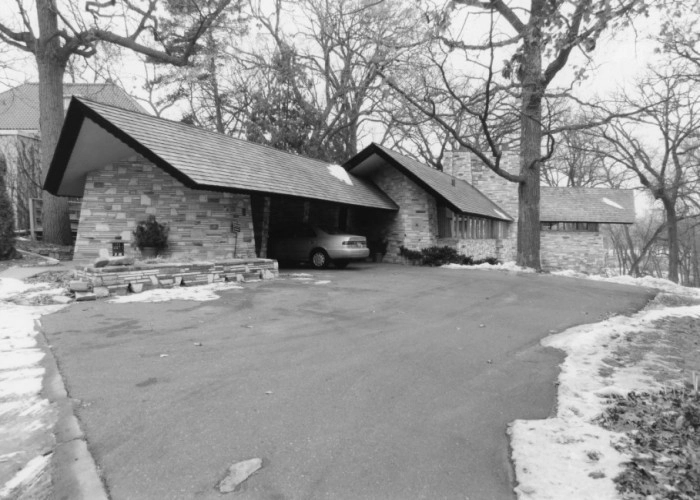
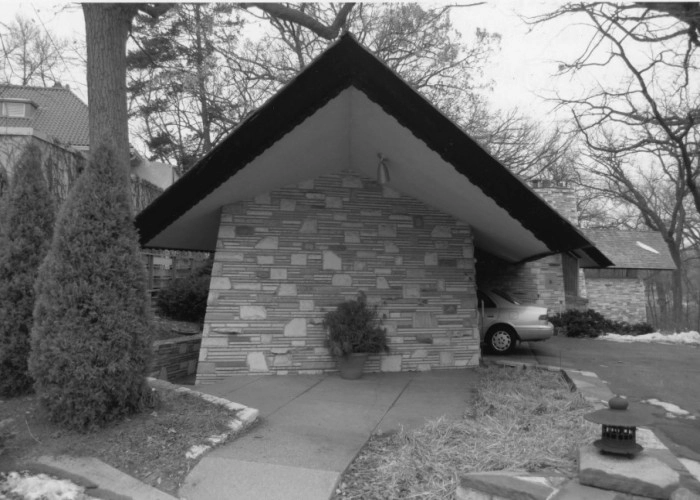
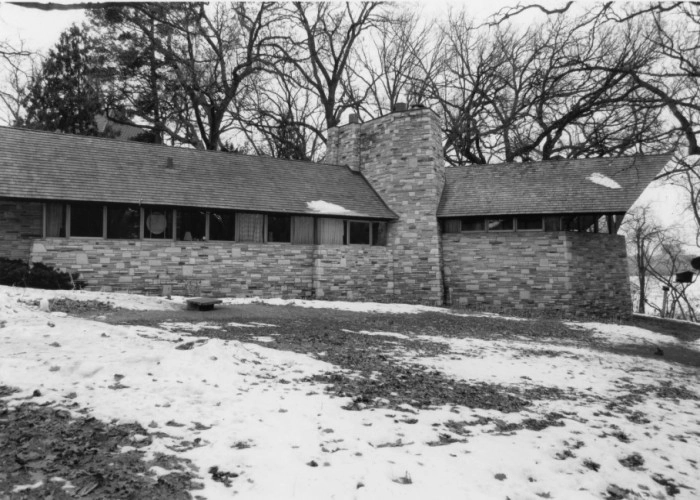
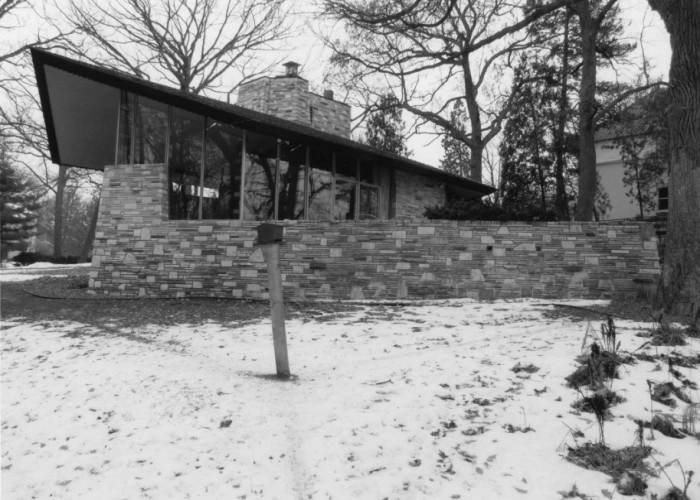
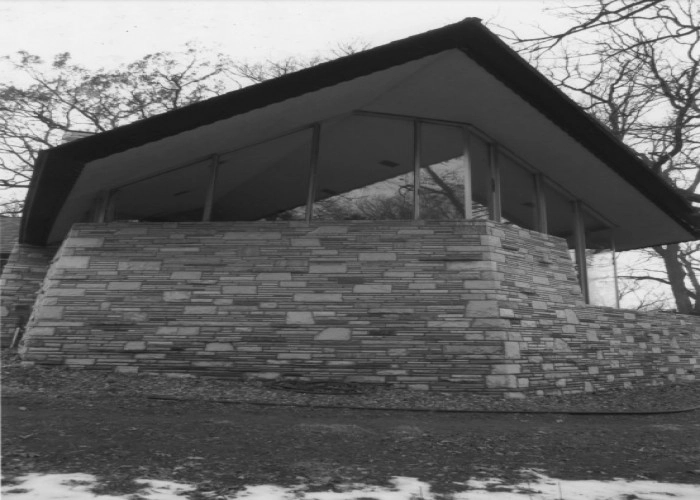
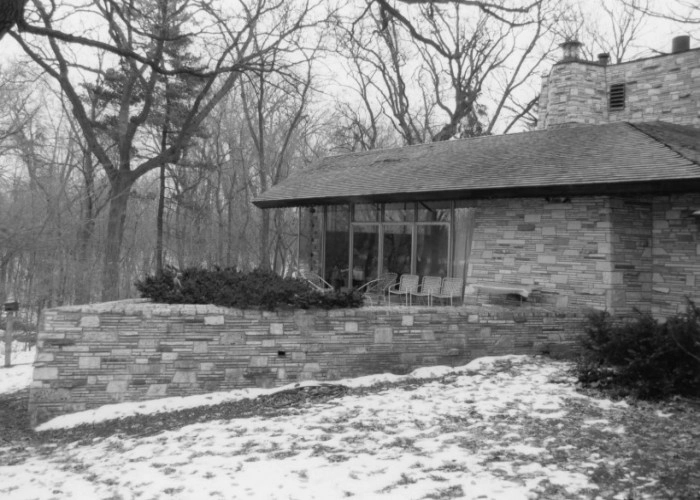
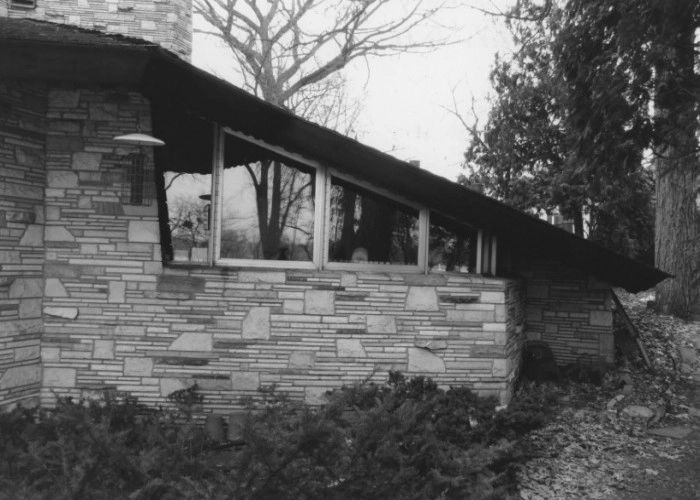
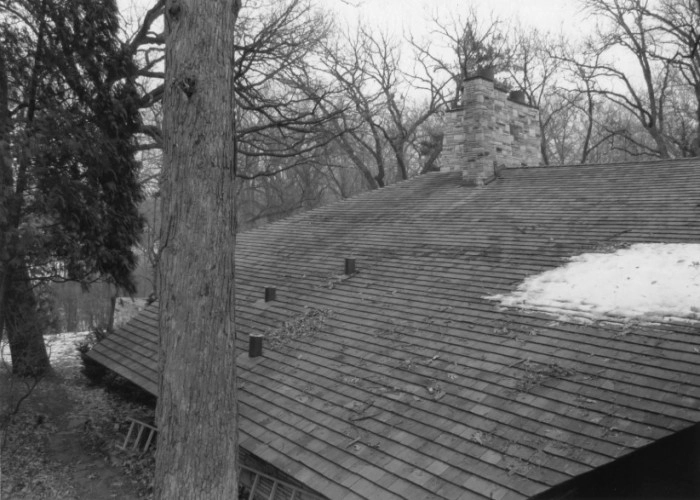
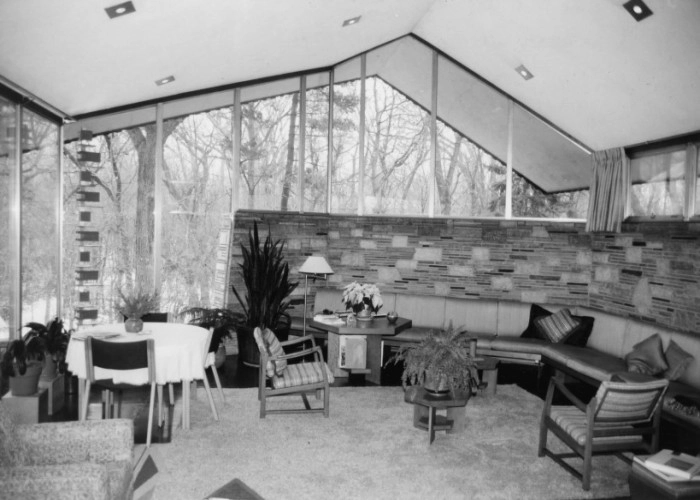
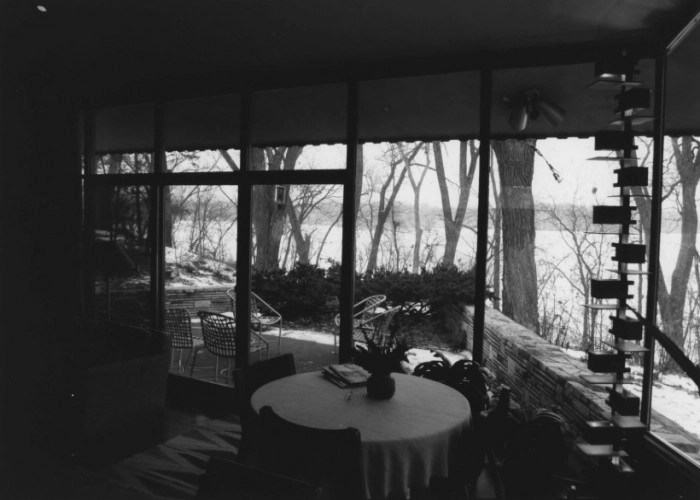
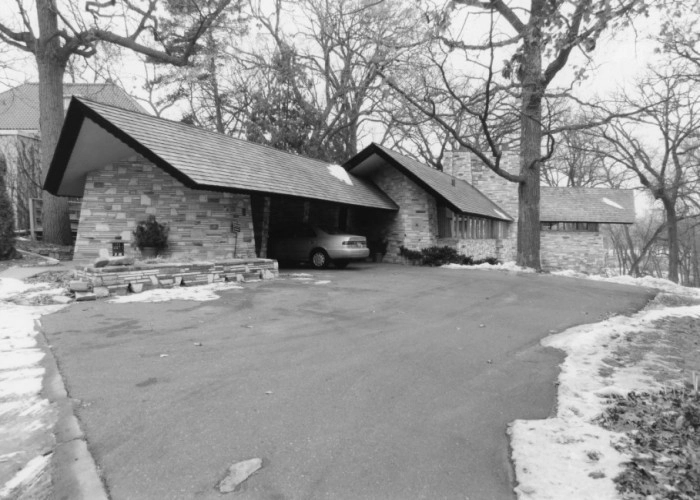
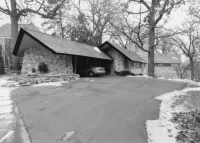
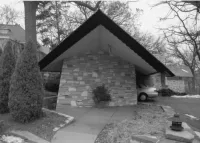
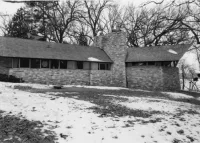
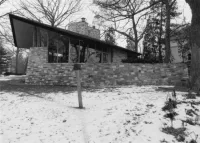
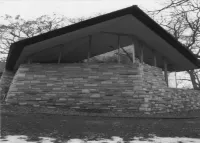
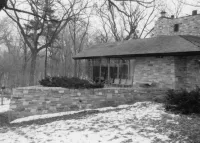
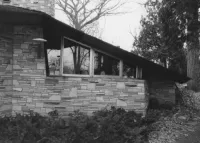
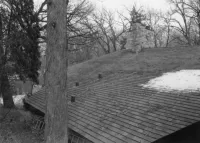
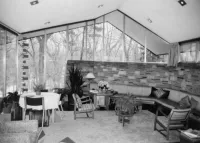
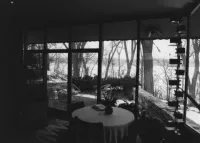
The Frieda and Henry J. Neils House - National Registry of Historic Places
Statement of Significance:The Frieda and Henry J. Neils House is eligible for the National Register under Criterion C as a property that embodies distinctive characteristics of a type, period or method of construction. It is of statewide significance in the area of architecture. The house is a good example of Frank Lloyd Wright’s post World War II Usonian houses. It is also a singular example because of its unique building materials - cull marble, clear Western larch and aluminum. It is the only house designed by Frank Lloyd Wright constructed of marble.’ Henry J. Neils, a prominent and well-connected Minneapolis businessman, not only suggested the unique building materials, but also was able to secure all of them through companies with which he was personally or professionally associated. The Frieda and Henry J. Neils House falls within the statewide historic context "Urban Centers, 1870-1940," and within the local contexts "Minneapolis Architecture: Post War Minneapolis, 1945-1991."
The singularity of the house is a manifestation of the well-documented process of give and take between Henry J. Neils and Frank Lloyd Wright that characterized the design and construction phases. The process of designing and constructing the Neils house, and discussions about building material selection, are meticulously documented in extensive correspondence between Neils and Wright. Such correspondence proved necessary because Wright did not visit the Neils house site until after the house was built, and Neils’s visits to Taliesin were infrequent. Neils also kept careful records of contracts and expenditures.
In 1949 Henry J. Neils, retired president of Flour City Ornamental Iron Company in Minneapolis, and his wife, Frieda Tetzlaff Neils, asked Frank Lloyd Wright to build a “one story modem functional house,” for them and their daughter Patricia, the youngest of their three children. They chose three lakeside lots that adjoined their 1923 thirteen-room family home at 2815 Burnham Boulevard in Minneapolis, as their building site.
The Neils’s decision to approach Wright was an informed one. Collectively, Frieda and Henry were extremely knowledgeable about the arts, design, architecture, the building trade, and construction. Frieda Tetzlaff, Neils was the daughter of Eugene Tetzlaff who founded Flour City Ornamental Iron Company in Minneapolis in 1893. She frequently made extended visits to Europe with her parents where she became very interested in modem decorative arts and architecture. She was an avid collector of decorative arts, notably Meissen, Dresden, Venetian glass, and later Japanese and American ceramics. She was also a great admirer of the architecture and philosophies of Frank Lloyd Wright, and read widely on the subject. She suggested to her husband that Wright design their new home." Henry J. Neils was familiar with the building trade and accustomed to working with architects, contractors and craftsmen in his capacity as president of Flour City Ornamental Iron Company, a company that specialized in architectural metalwork and curtain wall windows, and which was also known for its artistry. Additionally, he was a scion of the J. Neils Lumber Company, founded by his father Julius, in Cass Lake, Minnesota, and a trustee of Northwestern Marble and Tile Corporation, Minneapolis. Although he once wrote to Wright saying, “Mrs. Neils and I are rank amateurs at this kind of work,” the correspondence suggests this was not the case.
In an effort to connect with Wright, the Neilses sought the counsel of Dean and Mrs. Malcolm Willey, for whom Wright designed a house in 1934 in the Prospect Park neighborhood of Minneapolis.’ The Willey House was an important commission for Wright for several reasons. It was his first commission after years without work during the late 20s and early 30s, and ushered in a period of tremendous achievement and productivity for Wright; his very next commission was Fallingwater. But most significantly, the Willey House “represents the major bridge between the Prairie style and the soon-to appear standard L-plan Usonian house.” Mrs. (Nancy) Willey suggested they contact Eugene Masse link, Wright’s secretary, for an appointment with the architect. Prior to the arranged meeting, Neils sent Wright a letter in which he stated, “Mrs. Neils and I feel that only you could design a house that would take the best advantage of the beautiful view over Cedar Lake, On October 16,1949, the Neils’s and their elder daughter, Mary McGee, traveled to Taliesin in Spring Green, Wisconsin to meet with Wright. Upon showing Wright a photograph of their 1923 Mediterranean-style home, the architect immediately agreed that a new house was in order commenting, “You sure do need a new one; why don’t you bum the old one down? When asked by Wright what their requirements were for their new home, the Neils’s listed, “one level. a large living room, three small bedrooms each with a private bath, a kitchen and a carport.*’ They also specified a $25,000.00 maximum budget. On November 6, Wright sent a letter agreeing to take on the project.
In a lengthy November 10th letter to Wright, Neils once again reiterated the family’s spatial requirements, and also described certain intangible qualities he sought in the design explaining, “As you know I am a lover of nature and enjoy the trees, water and beautiful sunsets over the lake. If the beautiful outdoors can be brought inside, this effect will give me a great deal of satisfaction.” He also added, “If you should decide on the use of aluminum, bronze, stainless steel, or just plain iron, our company is in a position to furnish such items. I am thinking particularly of window frames and mullions should the use of metal fit into your scheme of construction.”
The Neilses were pleased with the plans they received from Wright in March of 1949. “You have interpreted our requirements perfectly,” Neils wrote. In the same letter Neils offered to “secure the necessary lumber from my brothers who operate a lumber mill at Libby, Montana and Klickitat, Washington,” listing Ponderosa pine, fir, larch, tamarack, some cedar and white pine as possible choices. He also reiterated his offer to fabricate aluminum windows and glazed doors at Flour City Ornamental Iron. “[Flour City owns] the dies for aluminum extrusions that will accommodate double strength, plate or thermopile glazing.”
Wright’s design for the Neils house is rooted in his principles for “Usonia,” a democratic societal ideal for which the architect designed Usonian, or “affordable, beautiful housing for a democratic America,” specifically the American middle class. *^ In his 1943 autobiography, Wright stated that his Usonian houses were intended to, “liberate the people living in the house.” In order to do so he challenged his clients to “see life in somewhat simplified terms,” and believed it was “necessary to get rid of all unnecessary complications in construction.” The Usonian house was modularly planned on one level, and organized spatially into active and quiet areas, which Wright segregated using various, angled geometric floor plan configurations. Usonian houses featured dominant living rooms often with a window wall on one side, and a masonry “workspace,” or kitchen, and utility core. Wright eliminated basements as well as garages, which he replaced with more economical carports. Structurally, the Usonian house stood on a concrete slab within which gravity heating was integrated. Wright felt it was ideal to “complete the building in one operation as it goes along the house is finished on the inside as it is completed outside.” To this end he employed sandwich wall construction, and favored five construction materials: wood, brick, cement, paper and glass.
The Herbert and Katherine Jacobs Residence (Jacobs 1) built in 1936 in Madison, Wisconsin, was the first of Wright’s built houses that he described as “Usonian” The L-shaped plan of the house accommodates quiet areas in one wing and active in the other, and includes a large dominant living room, and masonry workplace core at the intersection of the two wings. The house, which cost $5,500. to build, was constructed of relatively inexpensive materials including brick, redwood and pine boards, and employed several efficient, low-cost building techniques, such as sandwich wall construction, and simplified, efficient design elements, such as gravity heating and a flat roof In that regard it is typical of the simply planned, inexpensively constructed Depression-era Usonians. Over time, however, Wright designed scores of Usonian houses that varied in composition and complexity with regard to geometry, size, materials, and structural elements. Wright also experimented with numerous roof configurations and cantilevers. While Depression-era Usonian houses featured inexpensive materials reflective of lean economic times, “masonry construction became the standard after WWI.”
In plan, the Neils House bears many of the hallmarks of Wright’s Usonian houses and in this regard is closely related to Wright’s first Usonian, the Jacobs I House. These hallmarks include modular planning, one-level construction, social and spatial organization of the house into active and quiet areas, dominant size and placement of the living room, a masonry workspace core, and concrete slab floor with integrated gravity heating. The plan was originally generated on a 4’0” modular grid but was later reduced to a 3’6” grid to reduce costs. The impact of the module reduction is evident in narrow “gallery,” or hallway passage and several compact rooms. The layout of the house is one of many variations of the in-line plan Wright used for his Usonian houses. Other characteristic features include integrated lighting and furniture, and a non-load bearing window wall.
Generally speaking, the more expensive building materials and masonry construction of the Neils house are typical of Wright’s post-World War II Usonians, which reflect postwar economic recovery, more generous home-owner budgets, and the commercial availability of an increasingly wide range of building materials. However, the Neils house is completely unique among Wright’s houses in the specific building materials used. The house is constructed of cull or scrap marble, clear Western larch interior tongue and groove walls, and custom-made aluminum windows and doors -- materials Wright never specified for his Usonian homes. All the materials were expensive on the retail market, and were either: unusual or not readily available (cull marble); not generally used for the purpose employed in the Neils house (clear Western larch for interior walls); or were used in commercial, not residential, construction (die-extruded aluminum windows and doors.) Uniquely, all three of these unusual and expensive materials were readily - and affordably - available to Henry Neils through three companies with which he was personally or professionally associated. They are respectively: Northwestern Marble and Tile Corporation, of which Neils was a trustee; the J. Neils Lumber Company, founded by Neils’s father Julius, and operated by two of his brothers, and; Flour City Ornamental Iron Company, founded by his father-in-law, Eugene Tetzlaff, and of which Neils was president. Through this fortunate set of circumstances, these more expensive and unusual construction materials proved to be the most economical and accessible choices for the house. Although it cannot be discerned precisely from the correspondence which materials Wright originally specified for the house, Mary McGee recalls fieldstone, brick, concrete block, and Tidewater cypress being mentioned in conversations. However, it can be discerned that Henry Neils repeatedly suggested materials and products, and forwarded pertinent product literature and material samples to Wright on a regular basis. Wright and Neils’s choice of materials, and the availability of these materials for residential construction, link the Neils house to post World War II economic prosperity, and identify it as a postwar Usonian.
The most distinctive features of the house are the cull marble bearing walls and the process through which they were realized. Wright was receptive, but needed to be convinced, that cull marble could and should be used for the double or sandwich wall construction of the house. Frieda and Henry Neils set out to convince him. They went to Northwestern Marble and Tile Corporation and examined “piles of marble culls,” left over from myriad major construction projects, such as federal buildings (including the Minneapolis Post Office), courthouses, banks (including the Northwestern Bank building in Minneapolis) and hotels, undertaken by the firm. They selected nine samples of marble to send to Wright for consideration. The samples included Roman Travertine, Gray Tennessee, Montana Travertine, Colorado Travertine, Rose Bonnard, Batticon, Radio Black, Carthage and Verde Antique in pieces measuring fi-om 2” - 12” wide and from 6” to 30” long. In a succinct note Wright responded: “Regarding the marble. Take over all larger chunks and larger pieces (see drawing forwarded) and mix. Make a model wall and send photographs.” Wright approved the sample wall shortly thereafter.
Wright eventually designed a double wall system lined with 2-inch rigid cork insulation. As constructed, the walls can’t, or taper from the ground up being approximately 30 inches thick at the bottom of the wall and 7 inches at the top. Wright also directed the stonemasons to roughly chip away the polished edges of the cull marble pieces to minimize the smooth and shiny appearance of polished block surfaces and edges. Stonemasons accomplished this labor-intensive step on site, one block at a time, by hand. Furthermore, Wright required the mortar be raked horizontally only to minimize any verticals. Although the walls were built to Wright’s specification, when the house was finished both architect and client expressed displeasure at the light color and visual dominance of some of the marble blocks. On Wright’s instruction, Taliesin apprentice John DeKoven Hill was dispatched supervise the hand staining of selected offending blocks. Although the applied coloration has faded on the exterior blocks, traces remain on some interior blocks.
The clear Western larch was another unusual choice of wood for the house. Larch, a pinewood, was not commonly used for interior residential paneling. Rather it was more often used commercially, or for flooring and decking because of its durability. Additionally, the larch chosen was relatively rare being clear, or free of knotholes. This made the choice both particularly distinctive and potentially more expensive — were it not for Neils’s family lumber business connections. Although Neils initially priced out Tidewater red cypress, a wood Wright favored and suggested for the paneling, on more than one occasion he told Wright he could secure larch at less than half the cost of cypress through his brothers at J. Neils Lumber Company. Neils respectfully wrote Wright: “the choice of wood Mrs. Neils and I will leave entirely to you. We know you are interested in getting a certain result and if the larch will not produce it, of course, we will not use it. But diplomatically continued, “If, however, larch is satisfactory we can make quite a substantial saving in the cost of the house.” A week later Wright approved the use of larch.
Neils was also responsible for the choice of aluminum for the windows and doors, prevailing over Wright’s preference for redwood. Once again, Neils was able to suggest a superior and affordable product that he, as president Flour City Ornamental Iron Company, could deliver. As early as March 1949, Neils made the connection between the number of windows and doors and their variety of shapes and sizes, and the wisdom of designing and fabricating them in aluminum. Although Flour City was producing window walls for large commercial projects across the nation, they were not in the residential window business. However, Neils told Wright that Flour City had “the necessary dies for aluminum extrusions that will accommodate double strength, plate of thermopile glazing.”^* He further stated that the installation of aluminum doors and windows in the Neils house would “undoubtedly be a tribute to our company.” Flour City also provided stainless steel counter tops in the kitchen (at Mrs. Neils’s request) replacing the linoleum countertops specified by Wright.
Much of the spatial dynamism of Wright’s design for the Neils house is derived from visual illogic of the load of the roof being supported by an unbroken expanse of light aluminum window that rise to meet the roof and wrap the north and east living room walls. The design presented technical challenges that were further complicated when Wright revised his original plans by removing a marble structural pier from the northeast comer of the living room. Wright pushed the structural drama to its limit when he specified that the mullions must “present thin edges to view and be as light in appearance as possible. It fell to Flour City window designer George B. Melcher and general contractor Lyle Halverson, vice-president and general manager of Madsen Construction Company, to find an acceptable solution.^® In the end, “stainless steel bars of sufficient size and strength,” used as mullions for the windows provided adequate structural support while maintaining a light appearance.
Originally, Wright designed a hipped roof or the Neils house, but later changed it to a gable roof with as5mimetrical planes. It is likely that Wright’s disdain of the house next door (the Neilses’s 1923 house) drove the redesign of the roof, as well as the orientation of the house on its site. Wright effectively blocked any view of the offending house by extending a section of the west plane of the gable roof to within inches of the ground. In a dramatic counterpoint, on the east side of the living room, the gable peaks seventeen feet above the ground and projects several feet beyond the window wall. The unequally sloped roof set up several unique conditions in the Neils house including the elimination of door-height soffits. According to Curtis Be singer, the Taliesin apprentice who prepared the working drawings for the Neils House, Wright often employed door-height soffits in his designs to establish “the intimate scale, horizontal layering of the space, its spatial contrasts, and the spatial continuity between the exterior and interior. In the absence of this ordering principle, the interior spaces have “increased plasticity,” and “a new sense of openness and freedom.” The absence of soffits also eliminated any space between them and the roof joists within which structural members could be concealed. As such, “any structural reinforcement of the roof-with steel beams or channels - now had to be handled within the roof thickness,” which is the case in the Neils house.
Although Neils told Wright in December of 1949 that he and Mrs. Neils “would like to avail ourselves of Section 3 of our contract with you under which you will send an apprentice to select the proper contractor and supervise the work until the structure is satisfactorily completed,” this did not happen. Eugene Masselink explained to Neils: “Mr. Wright does not know what advantage an apprentice would be to you at this time.” Instead, Neils interviewed contractors and hired Lyle Halverson and Madsen Construction Company as general contractors. Neils and Halverson supervised and troubleshot the construction of the house while constantly communicating with Wright by mail. The relationship between Taliesin, and Neils and the construction team in Minneapolis was close and productive. According to Mary McGee, “their ability to communicate was a major factor in the successful building operation.” At Taliesin, chief draftsman John Howe instructed apprentice John Geiger to undertake the Neils house working drawings, which Steve Oyakawa later completed. After Wright made revisions, apprentice Curtis Be singer redrew the working drawings.
Apprentice John DeKoven Hill worked most closely with the Neilses and was the only apprentice to visit the house while under construction. At Wright’s request, he supervised the staining of the marble blocks. But he also worked closely with the Neilses in his capacity as editorial director for House Beautiful magazine assisting with furniture and fabric selection. Hill was no doubt responsible for publishing photographs of the house in House Beautiful in November of 1955. The house was also photographed by several noted architectural photographers including Ezra Stoller, for Architectural Forum, and Pedro Guerrero, whose photographs appeared in House + Home.
Wright visited the house on three occasions. The first time was three and a half years after completion of the house, in October 1954, when he came to lecture at the University of Minnesota and was a houseguest of the Neilses.
The Neils house has had only two sets of owners - all members of the Neils family. Frieda Neils lived in the house until her death in 1975. Henry stayed on until 1977 when he remarried. In 1977 Mary McGee, elder daughter of Frieda and Henry Neils, and her husband J. Paul McGee purchased the house. Mary McGee currently resides in the Neils house.
The Neils house generated a second commission for Wright from the Neils family. In 1954, Wright designed a house for Patricia Neils Boulter and her husband Cedric Boulter in Cincinnati, Ohio.
The Neils house represents an excellent example of Frank Lloyd Wright’s postwar Usonian designs that evolved from his first Usonian, the Jacobs I house built in 1936, to the mature versions of the 1950s. Initially, straightforward plans and inexpensive materials characterized Usonian houses. After the Great Depression and the end of World War II, the designs increased in complexity and more expensive materials were often employed. The Neils house, through its complex massing, dramatic cantilevers, and the unique use of marble masonry. Western larch and aluminum doors and windows, represents a well-developed, important, and unique Usonian design by Frank Lloyd Wright from the postwar period.
Posted Date
Mar 09, 2022
Historical Record Date
Feb 05, 2004
Source Name
United States Department of Interior - National Park Service
Source Website
Delete Story
Are you sure you want to delete this story?